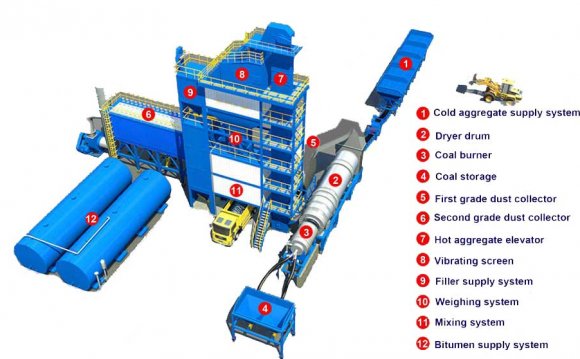
By Ed Misajet
Fred Prill does not pull any blows when the topic of brand new batch plant facilities is brought up in discussion. “Very couple of technicians with the exception of some inside extreme northeast want in group flowers anymore—at least not new people, ” says Prill, an equipment specialist with decades of expertise dealing with leading asphalt plant producers. “Batch plants, in their time, were the state for the art, really functional, and found the requirements of most asphalt manufacturers.”
Group plants, utilized during the change associated with century, had been easy in design. A one-ton group plant (60 tons each hour [tph]) was the normal size. The standard of the mix generated by these flowers found the specs of time. However, the standard of the mix produced was manually managed by the abilities for the plant operator. The main requirement in the early times ended up being for aggregate is totally covered with liquid asphalt. These requirements were shown when you look at the plant’s design. A typical group plant was designed with a hopper or bin to introduce the aggregate, a little dryer to warm the rock, hot displays to separate your lives the aggregate into several sizes, weigh hoppers to manage proportioning and a pugmill to blend the asphalt cement (AC) and aggregate.
Requirements Changed
As time went on, the requirements and demands changed and group plant design expanded more complex. During 1950s, interstate construction required hot mix asphalt (HMA) technicians to increase production capacity. Typical batch plant size risen up to six tons to generally meet manufacturing demands. Larger screens were added to accommodate producing numerous mixes. Otherwise, group plants changed little until about 30 or 35 years ago.
The major changes that adopted were the onset of automatic computer system batching settings, more cost-effective dirt enthusiasts together with introduction of rise silo methods. Flowers got a whole lot larger and cleaner. They added silos to reduce vehicle turnaround time. But flowers nonetheless produced one group at a time. Pricey pugmill mixers and multideck displays were still needed. They led to high initial expenses plus high maintenance prices, that have been the batch plant’s ultimate downfall.
Wave of the Future—Continuous Combine Asphalt Places
Continuous blend type plants emerged during the early 1970s as a viable choice to batch plants. A normal batch center produced 150 to 300 tph whereas constant combine plants created 300 to 500 tph. The first drum flowers capable of creating large tonnages had been parallel-flow design systems, where aggregate movement had been parallel into the way of this temperature origin.
Early parallel-flow drum plants had been built to be transportable due to market need. Acceptance of the design has also been due to some extent towards participation of this Boeing Corporation, one of the first makers regarding the parallel flow system. Even though the design had some inherent technical defects, the plant nevertheless sold.
One drawback was having less polluting of the environment controls. Parallel flow methods retained increased percentage of fines and moisture during the heating and mixing process, ultimately causing fairly dirty pile emissions.
Heat Controls
Another drawback to your parallel design had been the problem of controlling mix heat. A parallel circulation design is a decreased temperature plant naturally. This is really important since most methods like these are not so practical for urban applications where you will find much longer haul times, job waiting times and a higher portion of handwork needing higher blend conditions. Minimal temperatures plus large moisture retention when you look at the mix additionally equated to compaction difficulties, thus greatly reducing the operating ranges of paving teams.
Also, there is a growing using reclaimed asphalt pavement (RAP). Effective addition of RAP is inherently a higher temperature process to move temperature into virgin aggregate before RAP is introduced in to the combine. This became the final demise knell the parallel flow asphalt plant design because it caused more and more excessive emissions. Hefty hydrocarbons and relatively large particulate emissions eventually cannot be fixed during the drying and blending procedure. These issues could possibly be moderated however eradicated.
This example, subsequently, produced issues in baghouse. Moisture and hydrocarbons from heavy fuels, AC vapors and heated RAP could plug the enthusiast bags, diminishing the baghouse efficiency and might, sometimes, develop a baghouse fire risk. In order to solve these problems, plant makers needed seriously to improve the look.
Counter Flow Designs
Plant engineers started initially to work on problems including moisture, excessive emissions and superheating associated with the baghouse. They thought that a counter flow design would enhance plant performance.
The countertop circulation drum plant is perfect for aggregate to move counter toward temperature origin allowing for high aggregate temperatures and reduced stack temperatures. This design along with innovations eg flighting methods, conveying systems, and burner design improvements solved the problems of earlier drum plant designs.
Contemporary counter movement designs feature an all in one drum mixer where aggregate is heated, liquid asphalt is included and RAP alongside additives tend to be included in one chamber. Various other designs consist of expanded recycling collars, separate post-dryer blending systems and batch plant retrofits. A few of these styles are predicated on the usage of large RAP contents and eliminating blue smoke within the exhaust bunch.
Learning how to Make Use Of RAP
Today’s requirements are greatly not the same as whenever drum mix plants very first arrived to usage. “during the early days, utilizing RAP had been revolutionary, but challenging, ” claims Prill. The RAP had been coated with asphalt and included moisture. Whenever RAP ended up being introduced to the mix procedure, problems eg vapor explosions, cooking the asphalt or extreme heat falls could happen.
As knowledge was gained using RAP, producers could actually develop plant styles which minimized the difficulties and supplied HMA producers the capability to manage RAP effectively.
Superpave and Changed Binders
A substantial development for HMA manufacturers within the last several years may be the introduction of Superpave and changed asphalt binders. These products produced some new challenges for plant manufacturers. Pumping and keeping some customized binders required plant changes. Sometimes, extra storage space tanks were had a need to hold the new Efficiency Grades or even the additional asphalts found in mixes containing RAP. Some customizations associated with the dryer’s flights had been needed to carefully dried out the coarser Superpave aggregate blends. After doing a couple of tasks, HMA manufacturers have, for the most part, discovered to handle the latest materials.
Silo Systems
“All of the drum plant technology in the world suggests nothing if not for the utilization of the silo system. They're going in conjunction. Some modern-day drum plants have production rates more than 600 tph. In the event that you don’t have a viable silo system, you will be still limited by how quickly your vehicle turnaround is, ” according to Prill. All drum plants utilize silo systems, some in groups of up to eight silos.