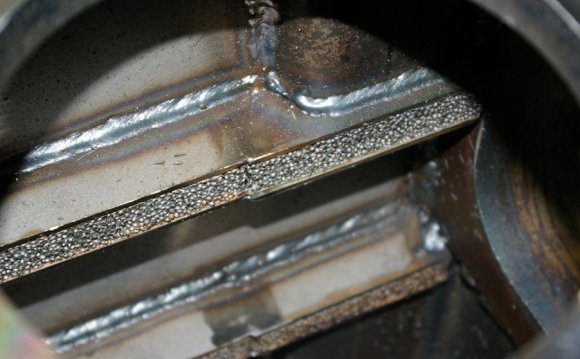
Making light work of machining - Milling device for lightweight building plastic materials controlled by Siemens CNC
Products employed for lightweight building are changing steel in an escalating amount of various industries. The development of suitable device tools is complex, once the chips created during machining are electrically conductive, and might not only be responsible for causing a brief circuit and have detrimental results on health. Because of this, their efficient removal is critical. To deal with this dilemma, HG Grimme is promoting its gantry rotary dining table milling machine / inclined bed (G-DT-F/SB), a 5-axis milling machine controlled by a Sinumerik 840 D sI. The equipment is used for make of car elements manufactured from CFP.
In G-DT-F/SB, different extraction methods suction the carbon chips and dust produced along the milling contour through extraction holes within the clamping fixture, while a brush extractor clears the milling head. Also, an airborne dust extractor within the sealed-off device cabin ensures that the air is purified to 99.99 % by-passing through a filtration system, thereafter it flows returning to the building. As a particular percentage for the fine dirt nonetheless handles to escape from the device and one chip could cause a brief circuit, the control cupboards tend to be afforded unique protection by the creation of internal overpressure.
Equal focus on safety and efficiency
As another protection for operating staff, along with the removal system, the underlying design regarding the device as a double gantry with inclined sleep ensures that operators are not needed to set base into the work space during manufacturing. Instead, they are able to clamp an element for machining into place externally at one side of the device, while a second one is being machined in.
The considerable protection functions certainly not compromise the machine’s effectiveness: when you look at the G-DT-F/SB with double gantry and two milling heads, a workpiece is machined in a matter of nine moments – with a perform reliability of 0.08 millimeters, speed values of 3, 500 millimeters/second and traversing speeds of 55 meters/minute. These values are attained through exact control for the mechanical design aided by the very dynamic Sinamics S120 converter.
Alongside the G-DT-F/SB, the business in addition makes use of Siemens CNC manages in its machine resources and mold making devices, because with ShopMill they benefit from incorporated work action programming optimized specifically for the production of one-off components and ultra-small production runs.
Captions
HG Grimme SysTech GmbH has continued to develop a 5-axis milling device especially for machining CFP components which can be managed by a Sinumerik 840D sl from Siemens. Picture 1: Copyright HG GRIMME SysTech GmbH
One of the ways of eliminating carbon chips immediately in which they are produced is utilizing a brush extractor mounted during the milling head.
Because one carbon chip may cause a brief circuit, the control cupboard is as hermetically sealed as you possibly can and overpressure developed around during subsequent operation.