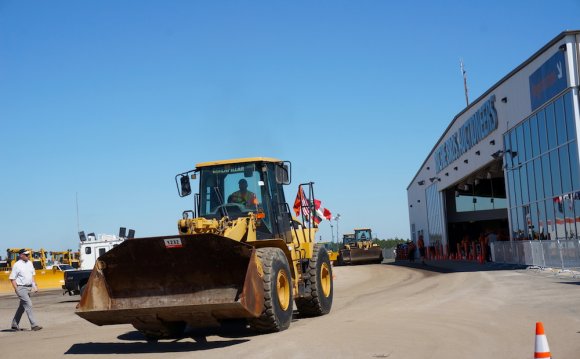
U.S. Army Corps of Engineers lifts and transports hefty precast cement shells for one-of-a-kind Ohio River lock and dam project with all the largest gantry crane, catamaran barge and strandjacks on earth.
By William Atkinson
All photos due to The U.S. Army Corps of Engineers, Louisville District.
You have to see this dam to trust it: the view of an innovative new, unique navigation task being constructed on the Ohio River near Olmsted, Ill., is, as you would expect, spectacular. Big precast cement shells are made on the shoreline at a specially created cement batching plant, precast cement facility and storage space yard. Precast shells are lifted and carried by a heavy-duty gantry crane to a ramp that transports all of them into the lake, where a catamaran barge lifts the shells and floats them with their last area inside river. Once positioned, the area underneath the shells is filled with tremie concrete. After that, much more concrete and metal frameworks are built atop the underwater precast shells. Impressive? What is even more impressive could be the dimensions and scope of this project, including 4, 700-ton (4, 260-tonnes) precast shells and the lifting ability for the gear, a number of the largest on the planet.
Maximizing American’s inland shipping
Built throughout the 1920s, many crumbling hair and dams regarding the Ohio River between Pittsburgh, Pa., while the Ohio’s convergence with the Mississippi at Cairo, Ill., have been replaced. Just upriver from Cairo tend to be Locks and Dam 52 and 53, built in 1929 and increasingly being changed because of the brand-new Olmsted Dam. This .1 billion project is composed of two 110-ft (34-m) x 1, 200-ft (365-m) locks; a dam composed of five tainter gates1; 140 boat-operated wickets2 that total 1, 400 ft (427 m) long; and a set weir. The full total construction would be 2, 700-ft (823-m) very long.
The U.S. Army Corps of Engineers (Corps), the project owner, awarded a 4 million building contract to a joint endeavor comprised of the Washington Group Global and Alberici Constructors (called WGA).
This strategic section of the Ohio River is the confluence associated with Ohio, Tennessee, Cumberland and Mississippi rivers. Much more water-borne tonnage passes this aspect than at any kind of place in America’s inland navigation system. Once Olmsted Dam is full in 2015 and working in 2016, it's going to enable tows to pass through this busy stretch of river in a single time, rather than the present five hours. The Corps estimates this task will produce financial advantageous assets to the nation in excess of $440 million yearly.
In-the-wet building: continuous shipping
Olmsted Dam features a approach to construction that'll not impair the movement associated with river during building. After learning a few dam-building techniques, the Corps decided to make the most of in-the-wet (underwater) building rather than the more conventional dry-cofferdam method. With this underwater strategy, precast layer parts tend to be transported while submerged in lake.
About 3, 300 pipe piles, 24 in. (610 mm) in diameter, at some point be driven for the entire dam foundation. Prior to final positioning, the precast layer foundation is more made by grading the riverbed to suit the shell’s geometry, making use of an aqua digger (a barge-mounted Komatsu PC3000). Once a shell’s basis tasks are complete, the final underwater set up begins. A catamaran barge, explained in subsequent text, moves the submerged precast shell into place for installation.
Hefty precast shells relocated with biggest gear
Large precast concrete shells are made on location at a specially created cement batching plant, precast center and storage space garden. The greatest shells measure 100 ft (30 m) x 125 ft (38 m) as they are 3-ft (0.9-m) thick. The littlest are 75 ft (23 m) x 100 ft and 2.5-ft (0.8-m) thick. Shells, including the lift framework, weigh anywhere between 3, 000 tons (2, 720 tonnes) to almost 5, 000 tons (4, 535 tonnes).
Before raising a shell from the casting sleep, a lifting framework is connected to the shell; the frame distributes the line lots from the raise points on the whole shell. Without having the frames, the reasonably slim shells (about 2.4-ft [0.76-m] dense) couldn't be hoisted without harm. The lifting frame additionally serves as a-work system when the shell is put in into the river. A normal lift framework is 75-ft (23-m) lengthy, 100-ft (30-m) broad and 45-ft (13.7 m) high.
After the lifting framework is attached to the shell, the layer is moved to the top a marine skidway by crane; this $9.5-million Super Gantry Crane, the greatest of the kind in North America, can carry around 5, 304 tons (4, 810 tonnes). The crane is wheelmounted, travels on metal rails and is with the capacity of moving the lifting frames perpendicular towards the rails. A self-contained bit of equipment, the crane operates down a generator. The top of the crane aids twelve strandjacks3 which are the main lifting mechanisms for the precast shells; each strandjack costs about $240, 000. The crane’s uppermost beams, generally strandjack beams, is hydraulically adjusted to various configurations.
The crane establishes the shell on a wedge-shaped steel framework with wheels, used to transport the layer along the skidway into catamaran barge during the river. The wedge form of the $4-million Cradle Transport gear program (CTE) keeps the shell horizontal while slowing action down the 8percent pitch. Whenever moving the loaded cradle regarding upper area of the skidway (in-the-dry), the CTE is affixed right to the cradle. Whenever cradle is usually to be lowered to the lake, it's closed in place on skidway (at a place just prior to being totally submerged) and disconnected from CTE. The CTE is then relocated up the skidway making sure that 500-ft (152-m) lengthy pendant extensions can be put in involving the CTE therefore the cradle. The pendant extensions make sure no hydraulic or electrical aspects of the CTE come to be submerged even though the cradle has been spotted from the skidway for running or unloading by the catamaran barge.
Catamaran barge largest of its type
As soon as the cradle achieves the end of the skidway, a $19-million catamaran barge, with an optimum ability of 4, 500 tons (4, 082 tonnes), moves into place. The lifting frame is connected to the barge and increased off the cradle from the barge. A towboat after that pushes the catamaran barge so the precast shell may set down with its permanent place into the lake.